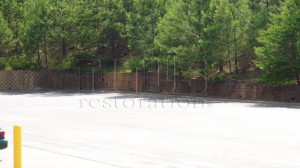
Retaining Walls
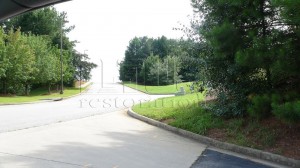
Steep Hills
Titus is often invited to visit building locations due to problems with floor covering failures caused by excessive moisture in the floor. It is typical that upon arrival to the building location, one site condition stands out as a glaring problem. Simply put, the building is located in a valley or on terraced building site and this fact has a tendency to create hydrostatic pressure in the slab.
Hydrostatic Pressure and High Alkalinity Cause Floor Covering Failures
Hydrostatic pressure increases floor moisture vapor transmission and increases alkalinity as salts on the concrete are moved to the surface of the slab. Nature is always seeking balance. Hot and cold mixed create warm. The dry air of an airconditioned space draws moisture from damp concrete. As the moisture passes through the concrete slab it also draws salts with it, thus creating a high pH at the slab/floor topping interface. Now there are two problems, 1) high moisture and 2) corrosive highly alkaline salts. Read about moisture tests for concrete.
See photos above of building sites that may be susceptible to hydrostatic pressure.
When a building is located on a low building site surrounded by hills on two sides it often times has problems with wet concrete. In an air-conditioned space with floor coverings, such as offices, it is probable that the floor coverings will have problems or fail. In a warehouse that is not climate controlled it is possible that the floor will sweat. This condition is called sweating slab syndrome, often abbreviated in the flooring industry as or SSS for short. Read about how to treat sweating slab syndrome in concrete.
Any building built on a terraced site which would have a tendency to have moisture problems. It is common that the site locations on terraced land have elevated hills on one or two sides with the flow of water toward a retention pond. It is not unusual for these hills to be 10 to 25’ higher than the finished floor level of the building.
As a simple rule of thumb, when a finished floor level is lower than the surrounding earthen grades, moisture vapor pressure increases at the rate of ½ lb per foot of graded drop. For example, a grade drop of 20 feet would create an increase of 10 lbs per square foot of moisture vapor pressure.
How to Install a Moisture Barrier for a Floorcovering
Moisture vapor transmission as it relates to a floor covering failure is a common problem. As a general statement, epoxy based moisture barriers are used and they typically require steel shot blasting, grinding the edges, and one or two coats of a moisture resistant epoxy coating system applied to the surface of the concrete prior to the floor covering installation.
Each floor covering material should contain specific method and material specifications to address high moisture when it is encountered. Titus recommends following the floor covering manufacturer’s instructions, including the instructions of all referenced documents when installing floor coverings.
Successfully treating high moisture in concrete slabs has been done on millions of square feet for decades. It is very common in the flooring industry, however, the moisture treatment will most likely change for each floor finish manufacturer. Most manufacturers specify their own systems or only systems they have tested and approved. Titus has found that there are many suitable moisture mitigating systems.
Titus recommends using moisture mitigation test methods, surface preparation methods, and products or systems in exact accordance with the floor covering manufacturers recommendations. A coated floor system, jute backed carpet, rubber backed carpet, glued carpet square, vinyl tile, etc may all recommend different moisture abatement treatments and different moisture testing requirements. Read about concrete moisture testing.
Mitigating Liability in a Floor Covering Failure
In conclusion, it is possible to successfully apply a 100% successful moisture barrier to a concrete floor and to successfully apply a floor coating or floor covering over that moisture barrier. There are several manufacturers of moisture barriers and many would work in any given situation, however, again, Titus recommends using only methods and materials specified by the finished floor manufacturer. Following the method and materials specifications of the floor finish manufacturer is the best way to create sole source responsibility.